How Can Quality Audit Lead to Continuous Improvement and Higher Growth?
Home / Quality Audit
One of the primary purposes of a quality audit is to drive continuous improvement. By identifying improvement areas and implementing corrective actions, organisations can enhance their management systems, meet quality goals, and reduce significant risks.
The landscape of businesses is evolving rapidly; so, it is important to make sure that all products and services by organisation thoroughly meet the established standards. For that, at the heart of this lies the quality audit which is an essential management tool and it evaluates the company’s quality management systems efficacy.
MMBA Accountants possesses a team of auditors, external and internal, to perform their audit duty diligently. Moreover, they are all-encompassing approach makes sure that your processes are compliant, and you are progressing in the right direction.
Table of Contents
Understanding the Basics of Quality Audits
A quality audit is a systematic and objective assessment of a company’s processes, products, or services. Other than this, it determines their compliance with defined quality standards, regulatory requirements, and customer expectations. Lastly, it is a cornerstone of quality assurance that aligns industry standards and contract commitments together.
Types of Quality Audits
There are three types of party audits:
First-party audits
These are internal audits. The company’s internal auditor or audit team conducts them. However the purpose is to assess the effectiveness of its quality systems.
Second-party audits
These audits are performed by a company on its suppliers. Through this audit, they evaluate the adherence to quality specifications and process specifications.
Third-party audits
An external auditor or a certification body conducts them. Also, these audits assess compliance with ISO 9001 standards or other regulatory frameworks.
Each type serves a distinct purpose, for example, self-assessment, making sure the supplier compliance or to achieve ISO compliance.
The Importance of Quality Auditing
The importance of quality auditing lies in making sure that processes, products, and systems are meeting the required standards and regulations. Additionally, it helps to identify non-conformances, risks, and marks areas for improvement. It also promotes efficiency and customer satisfaction. Lastly, it helps to build trust with stakeholders by affirming a commitment to maintain high-quality standards.
A Step-by-Step Guide on Quality Audit Process
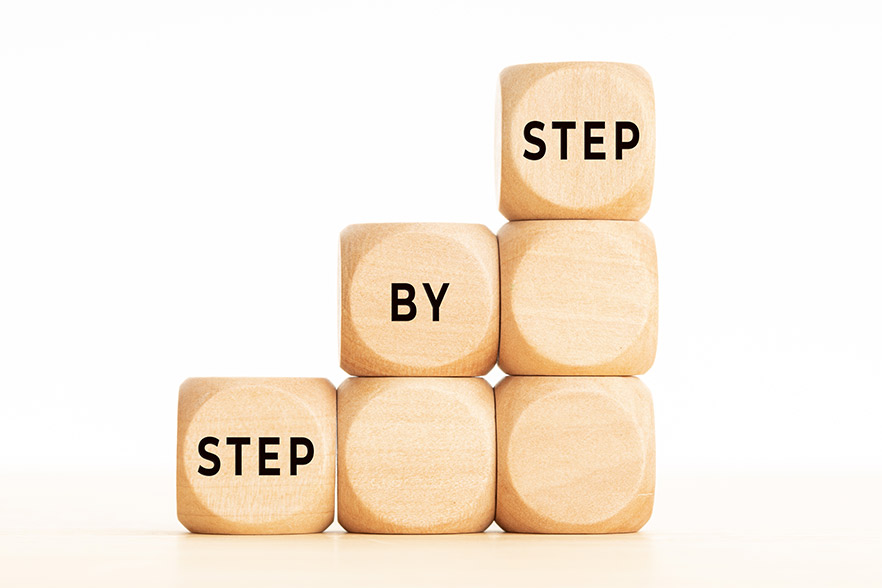
The quality audit process typically consists of several key stages:
Audit Initiation
The process begins with audit initiation. In this, they define the scope, objectives, and criteria. Moreover, the lead auditor assembles an audit team. However, it is important to confirm that they possess the necessary expertise.
Audit Planning
During planning, the audit team reviews the company’s quality systems, relevant documents, and work instructions. This stage involves a risk assessment— it prioritise high-impact areas for a focused approach.
Audit Execution
The audit execution phase involves a few important steps, for instance, gathering objective evidence through interviews, process observations, and to review document. This step assesses compliance with industry standards, regulatory requirements, and company policies.
Audit Reporting
The findings from the audit are documented in a comprehensive audit report. This report highlights audit findings—improvement areas, significant risks, and non-compliance.
Follow-Up and Corrective Actions
The audit ends with follow-up activities. It makes sure that they implement corrective actions are effectively. This step is vital to foster a culture of continuous improvement.
Key differences between Internal and External Quality Audits
While both internal quality audits and external quality audits aim for compliance and quality management systems; they differ in execution and purpose.
Internal Quality Audits
Internal auditors or the organisation’s audit team conducts them:
- It identifies improvement opportunities within the organisation’s processes.
- It helps align company policies with quality goals.
External Quality Audits
Third-party auditors or certification bodies conducts them
- It assesses the company’s adherence to regulatory requirements and external quality standards.
- Often linked to certifications, such as ISO.
- Both types play a crucial role in achieving continuous improvement and ensuring product quality.
Both the internal auditor and external auditor play a crucial role in maintaining the transparency of organisation’s through their expertise and experience.
The Role of the Auditor in Quality Audits
The role of the auditor is pivotal in the success of a quality audit—they are responsible for:
- To maintain objectivity and impartiality during the objective assessment.
- It collects and analyses data to produce meaningful audit results.
- Providing actionable recommendations to improve company’s quality management and ensure compliance.
For industries like medical devices, where strict quality management and process specifications are critical, the auditor’s expertise impacts overall product quality. Be it internal auditor or external auditor, their audit expertise helps in streamlining organisation’s processes a great deal.
Common Reasons for Quality Audit Failures
- Despite its importance, quality audit failure is not uncommon. Some common reasons for quality audit failures include:
- Lack of preparation during audit initiation.
- Inadequate documentation or outdated work instructions.
- Failure to address audit findings from previous audits.
- Insufficient engagement from other departments during the audit process.
These challenges underscore the need for a robust approach to audits, for example: collaboration across other departments and a commitment to continuously improve.
What is a Quality Audit Checklist?
A Quality Audit Checklist is a structured tool to assess the products specified quality standards processes, systems, or. It is a way to check compliance with regulatory requirements, internal policies, and customer expectations. In this, all critical aspects are reviewed, and this makes audits more consistent and effective.
Key areas covered in a quality audit checklist typically include:
- Documentation
- Process execution
- Employee training
- Resource adequacy
- Product quality
- Customer feedback
The checklist also helps record observations, findings, and evidence, enabling auditors to highlight non-conformances and suggest corrective actions. Moreover, a scoring system, such as “Compliant,” “Non-Compliant,” or “Needs Improvement,” is required and this gives clear results. The audit findings are then used to assigns responsibilities and timelines to address the issues.
Overall, a quality audit checklist is a vital component of any quality management system. It promotes continuous improvement by identifying risks and inefficiencies; so the organisation can resolve them for a better quality.
Organisations that invest in internal audit enjoy numerous benefits, including:
Conclusion
In an era of heightened competition and regulatory scrutiny, quality audits are an indispensable tool for organisations. From assessing compliance to identifying improvement areas, they ensure that businesses remain agile and customer-focused. By fostering a culture of continuous improvement, quality audits not only enhance company policies and practices but also contribute to long-term success.
Be it internal audits, external audits, or supplier audits, organisations must embrace the audit process as a pathway to excellence. With a clear focus on audit execution, reporting, and follow-up, companies can meet their quality goals, minimise risks, and thrive in today’s dynamic business environment.
FAQs
What is the primary purpose of a quality audit?
The primary purpose of a quality audit is to assess a company’s compliance with established quality standards and regulatory requirements. Moreover, it also identifies areas for continuous improvement.
What are the main types of quality audits?
The three main types are first-party audits (internal audits), second-party audits (supplier audits), and third-party audits (external audits conducted by certification bodies).
Why do quality audits fail?
Quality audits often fail due to poor preparation, outdated documentation, lack of engagement across departments, or failure to address findings from previous audits.
How do internal and external audits differ?
Internal audits are conducted by a company’s own auditors; they identify internal improvements, while external audits are performed by third-party auditors to assess compliance with external standards.
Why are quality audits important for compliance?
Quality audits make sure that you are adhering to industry and regulatory requirements, minimising the risks, and gradually improving product quality.